물류자동화의 ‘완성’ 돕는 몇가지 아이디어
‘알파고’의 바둑대결로 AI가 주목받게 되었듯이 2021년 3월 쿠팡의 뉴욕증권거래소 입성(86조원 시가총액 인정)은 일반 국민들의 물류에 대한 관심을 고조시켰다. 더욱이 의아했던 점은 당시 쿠팡의 적자 규모가 4조원에 달했다는 점이다. 한편 쿠팡 상장 1년 전 ‘우아한형제들’의 배민을 독일계 DH(딜리버리 히어로)가 4조7500억원에 인수하는 사건도 있었다. 창고와 트럭으로 대변되던 3D업종 물류가 핫한 주목을 받게 된 다이나믹스(Dynamics, 역동성)는 과연 무엇이고, 그렇다면 미래에도 물류는 계속 주목받는 산업으로 남게 될까? 역동적인 물류의 미래를 들여다본다. <편집자 주>
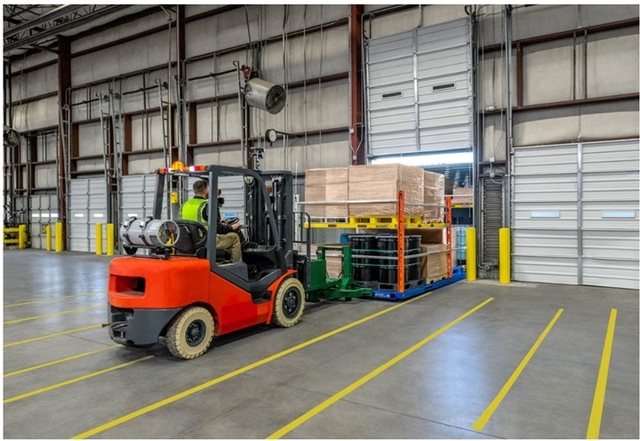
[뉴스투데이=김승한 (주)화물맨 부사장/경기대 겸직교수] 필자가 이전 자율주행 로봇 스타트업에 재직했었을 당시의 기억이다.
주력 제품군 중에 ‘무인지게차’가 있었고, 시연 때 무인지게차 자체의 성능에 대해서는 감탄을 하던 고객들이 실제 현장 도입을 결정하는 순간 주저하곤 했다.
주요한 원인은 무인지게차 이동의 앞, 뒤로 발생하는 로딩/언로딩(loading/unloading) 작업과의 연계성의 비효율이었다.
예로 카고트럭이 물류센터 독(Dock)에 도착하면 트럭에 실려 있는 여러 개의 팔레트를 끄집어내야 하는데, 무인지게차에 있어서 트럭 안을 들락날락하는 작업은 기술적으로 어렵고, 효율도 많이 떨어지는 작업이다.
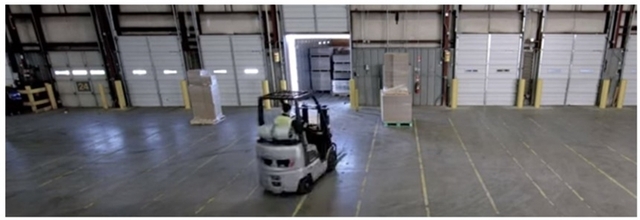
그렇다고 심리스(seamless)한 전체 자동화를 달성할 때까지 현장의 자동화를 계속 미룰 수는 없고, 당장 흔하게 마주치는 ‘부분’ 자동화의 안타까운 한계를 해결할 수 있는 방안은 정말 없을까?
몇 가지 관련한 아이디어 사례를 공유하고자 한다.
• 사례1. Dock 효율화를 위한 화물운반플랫폼(Freight Mobility Platform)
미국의 트럭회사 ArcBest社는 물류센터의 Dock 작업 효율성을 혁신적으로 높인 Vaux라는 이름의 장비플랫폼 출시를 발표하였다. 참고로 ArcBest는 지난 4년 동안 화물 취급 기술에 9천만달러 이상을 투자했다고 한다.
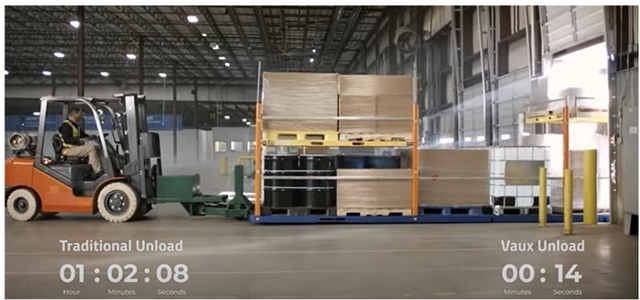
일반적으로 1대의 카고트레일러에서 화물을 싣고 내리는 데는 45분에서 1시간 정도가 소요된다. 하지만 Vaux를 사용할 경우 5분 이내에 상차 혹은 하차 작업이 가능하다.
Vaux는 H/W와 S/W가 통합된 이동플랫폼(Mobility Platform)이다. 우선 H/W는 트레일러 내부에 화물을 한번에 얹을 수 있도록 만든 강철 및 알루미늄 자재의 선반(Racking) 시스템이다.
지게차는 팔레트를 개별적으로 처리하는 대신, 지게차를 Vaux 플랫폼에 고정하여 화물 전체를 트레일러로 밀거나 한번에 꺼낼 수 있다. 마치 항공기 적재에 쓰이는 적재구조물인 ULD의 카고트럭용 확장판이라 보아도 무방할 듯하다.
추가적인 H/W로 커플러(Coupler)를 제공하는데 이는 기존 여러 모델의 지게차와 선반 플랫폼을 고정하기 위한 연결도구이다.
Vaux는 선반 시스템에 내장된 셀룰러 서비스와 GPS 추적용 소프트웨어를 통해서 화주에게 화물의 실시간 위치를 제공한다. 팔레트 적재시 팔레트 바코드 스캔도 할 수 있기 때문에 팔레트 단위 추적도 가능하다.
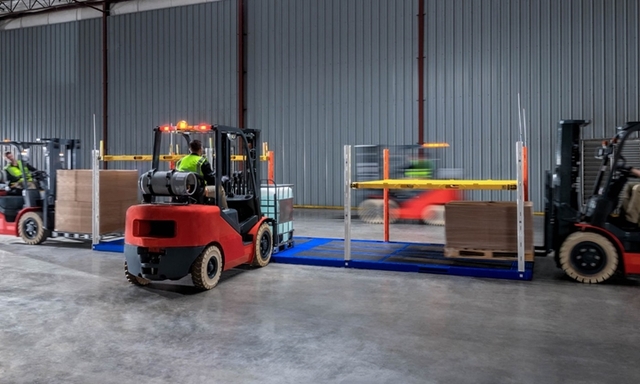
Vaux 운반플랫폼의 경우 Dock 내 견인 후에는 사방에서 복수의 지게차 협업이 가능하다. 이는 복수의 무인지게차 운영을 가정했을 때에도 매우 큰 장점이 된다.
즉, 여러 대의 무인지게차로 운반플랫폼에 화물 적재를 마치고 나서, 유인지게차 1대로 운반플랫폼을 접안되어있는 카고트럭 안으로 한번에 밀어 넣으면 된다.
카고트럭 내 적재라는 기술난이도 높은 작업은 무인지게차를 통한 자동화 대신 최소 지게차 인력 투입으로 해결 가능하다는 것이다. 전체 자동화에 대한 판타지에서 벗어나면, 현장의 자동화 도입 결정이 보다 수월해질 수 있다는 뜻이다.
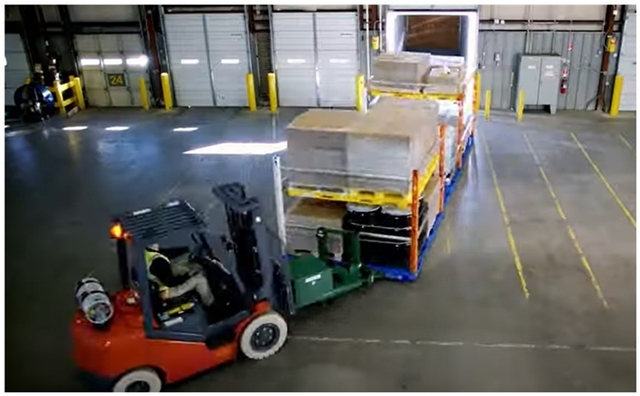
• 사례2. 웨어러블 장비 도입을 통한 혼합(Mixed) 팔렛타이징(palletizing) 해결
전 세계적으로 무인지게차가 가장 빨리, 많이 도입되는 영역을 꼽으라면 음료, 주류와 같은 제품군을 취급하는 물류 현장을 들 수 있다.
일단 이들 제품이 적재된 박스 혹은 팔레트의 무게를 감안할 때, 수작업 로딩/언로딩을 위해 많은 노동력을 투입하는 것보다 24시간 운영 가능한 무인지게차 등을 활용하는 것이 효과적이기 때문이다.
하지만 자동창고(AS/RS), 무인반송차(AGV/RGV), 각종 컨베이어 등의 자동화 장비로 구현된 최첨단의 스마트 물류센터 경우도 사실상 전체 자동화에는 한계가 있다.
예로 80~90%가 단일 품목의 박스로 구성된 팔레트 단위로 처리된다고 하더라도, 10~20%의 경우는 콜라, 음료, 주류 각 몇 박스씩을 섞어서 혼합 팔렛타이징(palletizing) 형태로 물류가 수행될 수밖에 없는 것이 현장의 모습이다.
그럼 10~20%를 위해 자동화된 혼합 팔렛타이징 워크스테이션을 별도로 구성한다는 것이 올바른 정답일까? 그렇지 않다. 이때는 차라리 수작업 인력을 보조할 웨어러블 장비를 검토하는 것이 더 타당한 해법이 될 수 있다.
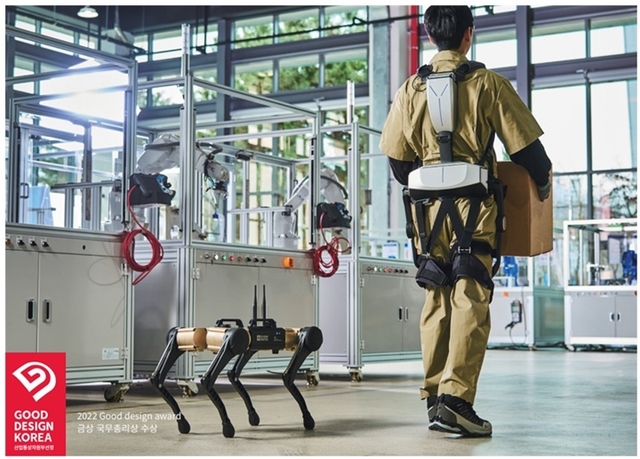
최근 출시되는 웨어러블 장비의 경우 단순히 근골격계를 지원하는 기본기능에 더해 주변 환경(소음, 분진, 화재 등) 및 작업자 상태(심박수 등)를 센싱하여, 자체 셀룰러 단말기로 중앙제어센터에 실시간 데이터를 전송, 빅데이터 분석을 통한 각종 정보 수집도 가능하다.
물론 작업자 간의 통신도 가능하고, GPS 장비로 위치 모니터링도 가능한 수준에 와 있다.
자동화의 성공은 부분 자동화/최적화로는 답을 찾기 힘들다. 전체적인 관점에서 자동화 ‘아일랜드’들을 엮는 교각을 찾고, 연결하는 것이 자동화의 도입과 성공을 보장하는 빠른 길이 아닐까 생각된다.
[정리=최봉 산업경제 전문기자]
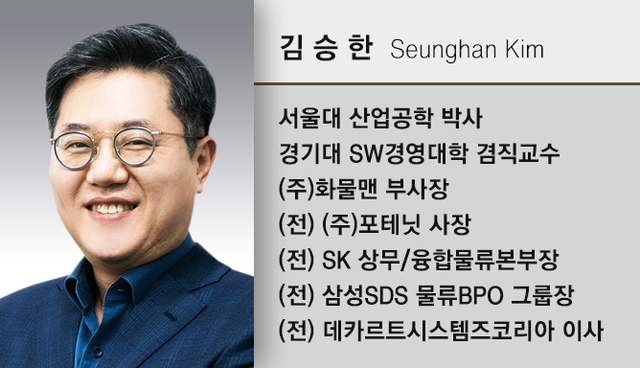